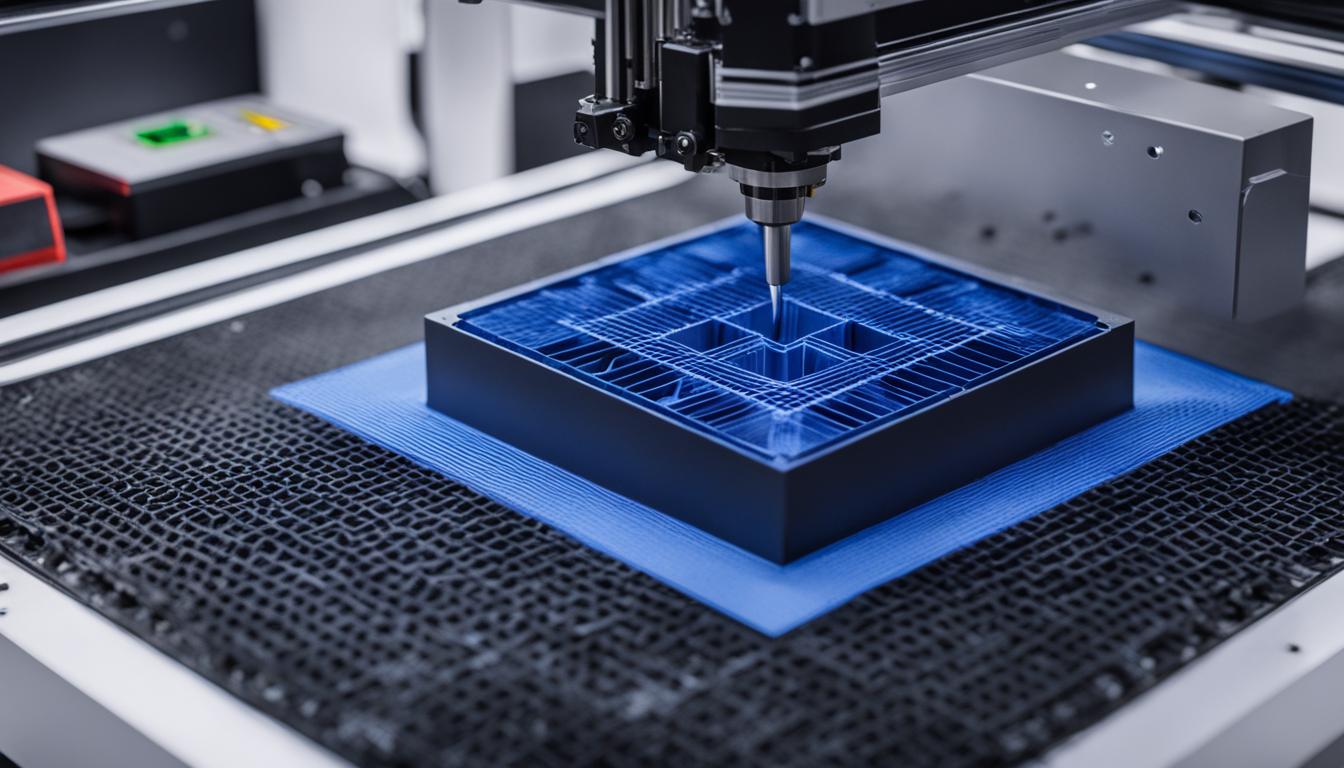
Das selektive Lasersintern (SLS) ist ein additives Fertigungsverfahren, das mittels Laserstrahlen dreidimensionale Objekte aus pulverförmigem Ausgangsmaterial herstellt. Dabei erfolgt das Schmelzen des Pulvers auf einer Bauplattform und ermöglicht die Erzeugung beliebiger Geometrien ohne Stützstrukturen. SLS, auch bekannt als Pulverbettverfahren, Laserschmelzen oder Laserstrahlsintern, findet häufig im Rapid Prototyping Anwendung, da es die Fertigung komplexer Teile mit hoher Präzision ermöglicht. Diese Technologie wird in verschiedenen Branchen wie dem Maschinenbau, der Automobilindustrie und der Medizin eingesetzt.
Der SLS-3D-Druck hat zahlreiche Anwendungsbereiche und wird in der Industrie zunehmend eingesetzt. Industriedesigner nutzen SLS, um Prototypen und mock-ups mit komplexen Formen und Geometrien herzustellen. In der Luft- und Raumfahrtindustrie wird die Technologie für die Entwicklung von Bauteilen mit hoher Festigkeit und Leichtigkeit genutzt. Im Maschinenbau und der Automobilindustrie ermöglicht SLS die Produktion von Funktionsteilen und Kleinserien. Auch in der Medizin findet das Verfahren Anwendung, beispielsweise bei der Herstellung von medizinischen Prototypen und Modellen.
Mit Hilfe von SLS-3D-Druckern können Unternehmen effizient und präzise Prototypen herstellen, um neue Produkte zu entwickeln und den Innovationsprozess zu beschleunigen. Dabei bietet das selektive Lasersintern zahlreiche Vorteile wie eine hohe Genauigkeit, die Fertigung komplexer Formen und die Möglichkeit der schnellen Iteration von Designs. Die Kombination aus SLS und Rapid Prototyping ermöglicht es Unternehmen, ihre Produktentwicklung zu optimieren und wettbewerbsfähig zu bleiben.
Geschichte und Entwicklung von SLS
Das selektive Lasersintern (SLS) ist eine Schlüsseltechnologie der Additiven Fertigung, die vor allem im Prototypenbau eingesetzt wird. Die Geschichte und Entwicklung von SLS geht zurück in die 1980er Jahre. Es wurde von Carl Deckard und Joseph Beaman an der Universität von Texas in Austin entwickelt und patentiert.
Eng mit der Firma DTM (Desk Top Manufacturing Corporation) verbunden, wurde SLS später von 3D Systems übernommen. Die Technologie erhielt Unterstützung von der Defense Advanced Research Projects Agency (DARPA), was zu weiteren Fortschritten führte.
Im Laufe der Zeit hat sich SLS zu einer Schlüsseltechnologie in der additiven Fertigung entwickelt. Durch die Kombination von Präzision, Geschwindigkeit und der Möglichkeit, komplexe Geometrien zu realisieren, ist SLS sowohl in der Industrie als auch im Forschungsbereich weit verbreitet.
Wie funktioniert der SLS-3D-Druck?
Beim selektiven Lasersintern wird das pulverförmige Ausgangsmaterial schichtweise auf eine Bauplattform aufgetragen. Mit Hilfe eines Laserstrahls wird das Pulver schrittweise geschmolzen und gesintert, wodurch das gewünschte Objekt entsteht. Das Pulverbett dient als natürliche Unterstützung für überhängende Strukturen, so dass keine Stützstrukturen nötig sind. Der Prozess ermöglicht die Herstellung komplexer Geometrien, da der Laserstrahl präzise gesteuert werden kann. Nach dem Drucken werden die Teile entpulvert und können je nach Bedarf nachbearbeitet oder lackiert werden.
Der SLS-3D-Druck basiert auf einem Verfahren, bei dem das Ausgangsmaterial in Form eines feinen Pulvers verwendet wird. Dieses Pulver wird schichtweise auf eine Bauplattform aufgetragen, wobei jede Schicht mit einem Laserstrahl geschmolzen und gesintert wird. Durch diesen Prozess entsteht das gewünschte Objekt in einer präzisen und kontrollierten Art und Weise.
Der Laserstrahl wird verwendet, um das Pulver zu schmelzen und zu sintern. Dadurch verbinden sich die Pulverpartikel miteinander und bilden eine feste Struktur. Das Pulverbett fungiert als natürliche Unterstützung für überhängende Strukturen, wodurch auf Stützstrukturen verzichtet werden kann.
Durch die präzise Steuerung des Laserstrahls können komplexe Geometrien hergestellt werden. Der Laserstrahl kann seine Intensität und Geschwindigkeit anpassen, um unterschiedliche Materialien und Geometrien zu verarbeiten.
Nach dem Drucken werden die Teile aus dem Pulverbett entnommen und entpulvert. Sie können je nach Bedarf nachbearbeitet oder lackiert werden, um die gewünschten endgültigen Eigenschaften zu erreichen.
Der SLS-3D-Druck bietet zahlreiche Vorteile, darunter die Möglichkeit, komplexe Geometrien ohne Stützstrukturen herzustellen, die hohe Präzision und die Vielseitigkeit bei der Verarbeitung verschiedener Materialien. In vielen Industriebereichen wie dem Maschinenbau, der Luft- und Raumfahrtindustrie sowie der Medizin hat sich der SLS-3D-Druck als effektive und effiziente Fertigungstechnologie etabliert.
Der SLS-3D-Druck hat das Potenzial, die Art und Weise, wie wir Prototypen und funktionale Teile herstellen, zu revolutionieren. Mit seiner Fähigkeit, komplexe Geometrien präzise und effizient herzustellen, ist der SLS-3D-Druck eine wichtige Schlüsseltechnologie in der additiven Fertigung.
Anwendungsbereiche von SLS
Das selektive Lasersintern (SLS) ist eine äußerst vielseitige Technologie, die in verschiedenen Bereichen der Industrie Anwendung findet. Vor allem im Industriedesign ermöglicht es die Herstellung von Prototypen und mock-ups mit komplexen Formen und Geometrien. Durch die präzise Steuerung des Laserstrahls können detaillierte und maßgenaue Modelle erstellt werden, die eine realistische Darstellung des Endprodukts ermöglichen. Dies ist besonders wertvoll bei der Evaluierung von Industriedesign-Konzepten und der Kundenpräsentation.
Auch in der Luft- und Raumfahrtindustrie hat das selektive Lasersintern seinen festen Platz gefunden. Hier wird SLS für die Entwicklung von Bauteilen mit hoher Festigkeit und Leichtigkeit eingesetzt. Durch die additive Fertigung können komplexe Strukturen optimiert und Gewichtseinsparungen erzielt werden, was für die Nutzung in der Luft- und Raumfahrt von großer Bedeutung ist.
Im Maschinenbau und der Automobilindustrie hat sich das selektive Lasersintern als effektive Methode zur Herstellung von Funktionsteilen und Kleinserien bewährt. Dank der Technologie können komplexe Teile direkt aus CAD-Modellen hergestellt werden, ohne teure Werkzeugkosten für die Herstellung von Spritzgussformen oder die Bearbeitung von Metallteilen.
Auch in der Medizin wird das selektive Lasersintern erfolgreich angewendet. Hier wird es beispielsweise zur Herstellung von medizinischen Prototypen und Modellen verwendet. Das Verfahren ermöglicht die Produktion von detaillierten und maßgenauen Modellen für die Planung von Operationen und die Entwicklung von maßgeschneiderten medizinischen Geräten.
SLS ist somit eine äußerst vielseitige Technologie, die in vielen Bereichen der Industrie eingesetzt werden kann. Von Industriedesign über Luft- und Raumfahrt bis hin zum Maschinenbau, der Automobilindustrie und der Medizin bietet das selektive Lasersintern eine effiziente und präzise Lösung für die Herstellung von Prototypen und Funktionsteilen.